Site testing or more specifically metal loss testing, is an important test that any integrator should perform to verify if a room can achieve a standard compliant (IEC 60118-4) hearing loop system.
What is Metal Loss?
When we introduce metal in close proximity to a loop it has a big impact and can mean we need to increase the power (which may mean a more powerful driver) or change the system type to compensate, for example using a loss control MultiLoop system.
Metal loss is caused by any conductive metal (including non-ferrous) that makes a closed circuit within the plane of the loop, in simple terms this is reradiating an opposing field and cancelling out some of the loop signal.
The most common causes are things like mesh reinforcement, raised access floor systems with metal tiles and suspended ceiling grids.
It causes an attenuation in field strength and loss of high frequencies which results in a dull or muffled sound. The severity is determined by how conductive the metal is and how close it is to the loop, as shown in this example video below.
In most cases the greater the loop width the more risk that the loop will suffer from greater metal loss. Past a certain size we also start to see increased variation of field strength across the loop. This is because in the centre of the room you’re furthest from the loop wire which is providing the direct field which we want to pick up, but surrounded by metalwork which is causing this cancelling effect. Variation can be unacceptable in rooms from 6m wide depending on the severity of the metal losses. In these cases, even with a more powerful driver you cannot achieve a compliant field strength across the whole room, there will be areas outside the ±3dB allowed in IEC 60118-4. This is where we use MultiLoop designs, with a series of smaller loop segments across the room that allow a consistent field strength throughout.
The length of the loop is almost irrelevant as long as the driver has enough voltage headroom to power it, when it comes to metal loss we are mostly concerned about the width of the loop.
Why is testing needed?
Without prior testing before install then the systems are specified based on average past data from similar construction types, e.g. a loop that is going to be installed on a floor made up of mesh reinforced concrete.
There is a careful balance between ensuring the system will work as expected and avoiding over-specifying with more powerful and costly loop drivers than the project may need.
Some typical metal losses for small loop widths are shown in the image below.
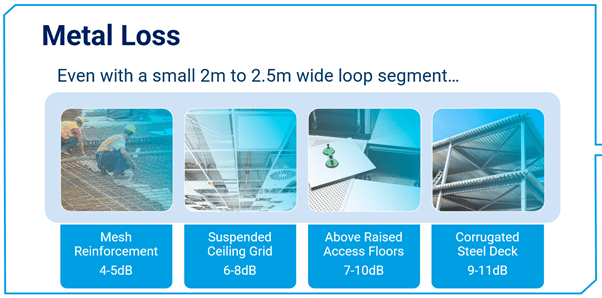
Testing before install is the only way to guarantee a system will perform as expected. At this stage it is important to note that the final construction needs to be in place, e.g. after raised floors are installed and the trial loop should reflect final loop in type (perimeter or a figure 8 for multiloop systems) and position. If installing in the ceiling the test loop must go in the ceiling.
Testing is most important when we have significant metal in the construction e.g. steel profile deck or raised access floor, or non-standard construction as the metal loss amount can vary. We have seen some projects with exceptionally high loss, or where the loss varies across the looped areas and have worked on projects such as loops being installed on ferries where testing was absolutely essential.
It is also important to note that testing can be integral to smaller scale projects too. For example even a counter loop may benefit from a prior test if the counter contains significant metalwork. We also always recommend testing when loops are being integrated into things like help points, exhibits, etc.
The results may show that you need a higher power driver than we would specify without prior testing or it may confirm that you can use a lower powered driver for the tested rooms. This could mean a significant cost saving on a larger project of 5 rooms or more. Site testing can also help us in other scenarios, for example when we have systems being installed directly above one another it is possible to measure the level of attenuate through the floor and ceiling structures. This way we can confirm if the systems can be used simultaneously without risk of overspill or crosstalk between them.
In one recent high profile project the floor had completely different construction in different areas of the floor. One area was raised access floor and the other steel sheet metal on a large raised steel frame. Metal loss testing showed we were seeing 9dB more loss in this area. Due to the test results we were able to design a flexible system with a second amplifier backing up the signal over this part of the loop to achieve a consistent and compliant signal throughout the whole room.
How to carry out a metal loss test
No matter what the system type is, it has never been easier to test a hearing loop system than with the HLS-2D. The HLS-2D driver uses a fixed current, has 4mm loop output connectors for test cable and can be powered from a 12V battery pack for ease of use on site. However, any driver can be used as long as you can measure the RMS current going through the loop.
Using the Loopworks R1 receiver and Measure app lets you record all the important test parameters and results in a specific Site Assessment test type. The results can then be used in Loopworks Design to ensure your system is allowing the exact amount of loss headroom required.
For more information and videos on the testing process please go to the links below:

Andrew Jackson
Ampetronic System Design Engineer
Andy Jackson has a BSc hons degree in popular music production. He has worked within the audio industry for 8 years and at Ampetronic for 6 years. As a system design engineer he specified systems for large installations around the world as well as providing technical support and training to distributors, consultants and installers. Andy has delivered technical training on our in house training course and at customer offices around the UK.